Boosting Productivity Through Lean Manufacturing Practices
Productivity improvement is crucial for staying competitive in today’s fast-paced business environment. Lean manufacturing, a methodology that focuses on minimizing waste and maximizing value, offers powerful tools to enhance productivity. By streamlining processes, reducing unnecessary steps, and optimizing resources, lean practices help organizations deliver higher quality products more efficiently. Techniques like the 5S system, just-in-time production, and value stream mapping are central to lean manufacturing, enabling companies to identify and eliminate inefficiencies. Emphasizing continuous improvement, lean practices not only boost productivity but also foster a culture of innovation and excellence within the workplace. Implementing lean manufacturing can lead to significant cost savings, improved customer satisfaction, and a more agile, responsive organization. In this blog would like to cover top 5 books on manufacturing productivity improvement and lean manufacturing practices.
1. “The Goal: A Process of Ongoing Improvement” by Eliyahu M. Goldratt
This book is a business novel that introduces the Theory of Constraints, focusing on identifying and managing bottlenecks in the manufacturing process to improve overall productivity.
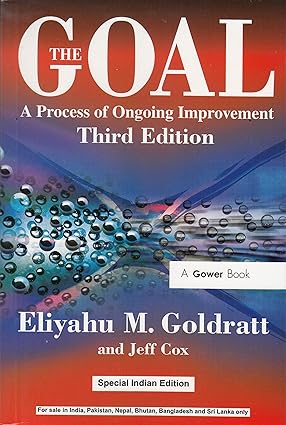
Summary of “The Goal: A Process of Ongoing Improvement” by Eliyahu M. Goldratt:
1. Focus on the Goal:
The primary goal of any business is to make money. All activities and processes should align with this overarching objective.
2. Theory of Constraints (TOC):
Goldratt introduces the Theory of Constraints, which posits that every system has at least one constraint that limits its performance. Identifying and addressing this constraint is key to improving overall efficiency.
3. The Five Focusing Steps:
1. Identify the system’s constraint.
2. Decide how to exploit the constraint.
3. Subordinate everything else to the above decision.
4. Elevate the system’s constraint.
5. If a constraint is broken, go back to step one.
4. Bottlenecks:
In a production process, bottlenecks (constraints) determine the pace of the entire system. Managing bottlenecks effectively is crucial for improving throughput.
5. Throughput, Inventory, and Operating Expense: Goldratt emphasizes three key performance measures:
– Throughput: The rate at which the system generates money through sales.
– Inventory: All the money invested in things the system intends to sell.
– Operating Expense: The money spent to turn inventory into throughput.
6. Continuous Improvement:
The process of ongoing improvement is vital. Once a constraint is resolved, the next one must be identified and addressed to continuously enhance the system.
7. Local Optimization vs. System Optimization:
Improving individual parts of the system (local optimization) does not necessarily lead to overall system improvement. The focus should be on optimizing the entire system.
8. Importance of Flow:
The book emphasizes maintaining a smooth flow of production, with the goal of maximizing throughput while minimizing inventory and operating expenses.
9. Role of Management:
Effective management involves identifying constraints, making decisions to address them, and constantly monitoring the system to ensure alignment with the goal.
10. Application Beyond Manufacturing:
While the story is set in a manufacturing plant, the principles of TOC and continuous improvement are applicable to various industries and business processes, including service and project management.
2. “Lean Thinking: Banish Waste and Create Wealth in Your Corporation” by James P. Womack and Daniel T. Jones
This book explores the principles of lean manufacturing and how they can be applied to reduce waste and increase efficiency in production processes.
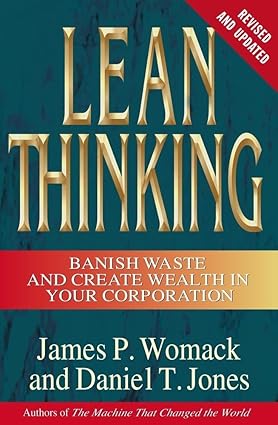
Summary of *”Lean Thinking: Banish Waste and Create Wealth in Your Corporation”* by James P. Womack and Daniel T. Jones:
1. Lean Principles:
– Core Concepts: The book introduces five key lean principles: specify value, identify the value stream, create flow, establish pull, and seek perfection. These principles guide organizations in eliminating waste and improving efficiency.
2. Value:
– Customer-Centric: Value is defined by the customer, and organizations must focus on delivering what the customer wants, when they want it, at the right price, and with the highest quality.
3. Value Stream Mapping:
– Identify Waste: Map out all the steps in the process of creating a product or service to identify and eliminate activities that do not add value, known as “waste.”
4. Flow:
– Continuous Movement: After removing waste, create a smooth flow in production processes where work moves continuously and without interruption from one stage to the next.
5. Pull System:
– Demand-Driven Production: Implement a pull system where production is driven by actual customer demand rather than forecasts, reducing overproduction and inventory costs.
6. Perfection:
– Continuous Improvement: The goal is to continuously seek perfection by regularly reviewing processes, eliminating waste, and improving quality and efficiency.
7. Types of Waste:
– Seven Wastes: The book identifies seven types of waste (overproduction, waiting, transportation, processing, inventory, motion, and defects) and focuses on strategies to eliminate them.
8. Empowering Workers:
– Involvement: Lean thinking emphasizes the importance of involving employees at all levels in the process of identifying waste and implementing improvements, fostering a culture of continuous improvement.
9. Lean as a Strategic Approach:
– Long-Term Focus: Lean thinking should be applied as a long-term strategy rather than a short-term fix, with a focus on creating value and building sustainable competitive advantage.
10. Case Studies:
– Real-World Examples: The book includes case studies from various industries to illustrate how lean principles have been successfully implemented to reduce costs, improve quality, and increase customer satisfaction.
These principles help organizations create more efficient processes, reduce waste, and ultimately enhance customer value and profitability.
3. “Toyota Production System: Beyond Large-Scale Production” by Taiichi Ohno
This classic book details the Toyota Production System (TPS), the foundation of modern lean manufacturing, emphasizing waste reduction and continuous improvement.
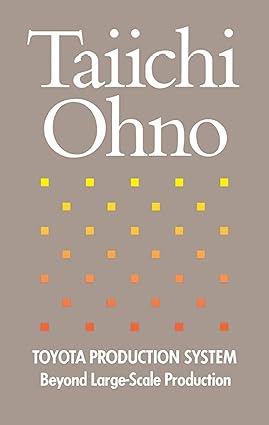
summary of “Toyota Production System: Beyond Large-Scale Production” by Taiichi Ohno:
1. Origin of the Toyota Production System (TPS):
– Background: Taiichi Ohno developed TPS as a response to the inefficiencies in mass production. Inspired by the need to do more with less, TPS focuses on eliminating waste and improving efficiency.
2. The Concept of Waste (Muda):
– Core Principle: Ohno identifies seven types of waste (muda) in production, such as overproduction, waiting time, and excess inventory, and emphasizes the importance of continuously eliminating them.
3. Just-In-Time (JIT) Production:
– Efficiency: TPS introduces the JIT philosophy, which means producing only what is needed, when it is needed, and in the amount needed. This reduces inventory costs and increases efficiency.
4. Automation with a Human Touch (Jidoka):
– Quality Control: Jidoka refers to machines that automatically stop when a problem is detected, allowing workers to address issues immediately. This ensures high quality and prevents defects.
5. The Pull System (Kanban):
– Demand-Driven: TPS uses the Kanban system to implement a pull-based production approach. Products are only produced in response to actual demand, reducing overproduction.
6. Continuous Improvement (Kaizen):
– Ongoing Process: Kaizen encourages every employee, from management to factory workers, to continuously seek ways to improve processes and eliminate waste.
7. Respect for People:
– Human-Centric: Ohno emphasizes the importance of respecting employees and involving them in problem-solving and decision-making processes. Employee empowerment is key to TPS success.
8. Flexibility in Production:
– Adaptability: TPS is designed to be flexible, allowing Toyota to respond quickly to changes in market demand without the need for large-scale production runs.
9. Customer-First Philosophy:
– Focus on Value: TPS prioritizes delivering value to customers by producing high-quality products efficiently. The system is designed to meet customer needs effectively and efficiently.
10. Global Influence:
– Impact: TPS revolutionized manufacturing worldwide, influencing lean production practices across various industries. Its principles have been adopted and adapted globally to improve productivity and reduce waste.
This book provides a deep understanding of the principles and practices that underpin the Toyota Production System, making it a key text in the study of lean manufacturing and operational efficiency.
4. “The Lean Six Sigma Pocket Toolbook: A Quick Reference Guide to Nearly 100 Tools for Improving Process Quality, Speed, and Complexity” by Michael L. George, John Maxey, David Rowlands, and Mark Price
This is a practical guide that provides tools and techniques from both lean manufacturing and Six Sigma for improving productivity and quality in manufacturing.
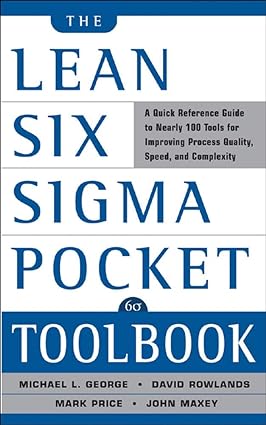
Summary of “The Lean Six Sigma Pocket Tool book: A Quick Reference Guide to Nearly 100 Tools for Improving Process Quality, Speed, and Complexity” by Michael L. George, John Maxey, David Rowlands, and Mark Price:
1. Comprehensive Toolset:
The book provides a concise reference to nearly 100 Lean Six Sigma tools, covering techniques for improving process quality, speed, and reducing complexity in various business operations.
2. Lean Six Sigma Integration:
It effectively combines Lean and Six Sigma methodologies, focusing on waste reduction (Lean) and process variation reduction (Six Sigma) to enhance overall efficiency and quality.
3. DMAIC Framework:
The book is organized around the DMAIC (Define, Measure, Analyze, Improve, Control) framework, guiding users on which tools to use at each stage of process improvement projects.
4. Clear Instructions:
Each tool is explained with clear, step-by-step instructions, making it easy for users to understand and implement the techniques in real-world scenarios.
5. Visual Aids:
The book includes diagrams, charts, and examples that visually represent the tools and techniques, aiding in quick comprehension and application.
6. Practical Applications:
Emphasizes practical applications of the tools in various industries, providing real-life examples and case studies that demonstrate their effectiveness in solving process-related problems.
7. User-Friendly Format:
The pocket-sized format and concise explanations make it a convenient quick-reference guide for practitioners, whether they are new to Lean Six Sigma or experienced professionals.
8. Focus on Process Improvement:
The tools are specifically geared towards continuous process improvement, emphasizing the importance of ongoing evaluation and refinement in achieving operational excellence.
9. Emphasis on Metrics:
The book highlights the importance of using data and metrics to drive decision-making, ensuring that process improvements are based on quantifiable evidence.
10. Versatility:
The tools are versatile and can be applied across a wide range of industries, from manufacturing to service sectors, making the book a valuable resource for diverse business environments.
This summary captures the essence of the book as a practical, accessible guide for improving processes through Lean Six Sigma methodologies.
5. “Kaizen: The Key to Japan’s Competitive Success” by Masaaki Imai
Kaizen, or continuous improvement, is a core concept in lean manufacturing. This book explains how Japanese companies have used Kaizen to enhance productivity and competitiveness.
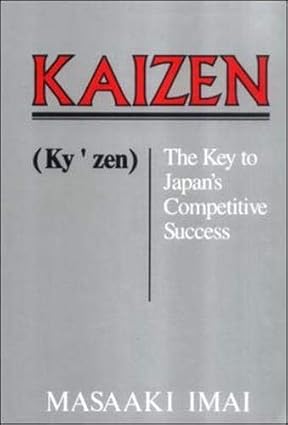
summary of “Kaizen: The Key to Japan’s Competitive Success” by Masaaki Imai:
1. Kaizen Philosophy:
– Continuous Improvement: Kaizen is a Japanese philosophy focused on continuous, incremental improvements in all aspects of life, business, and manufacturing.
2. Employee Involvement:
– Inclusive Process: Kaizen involves all employees, from top management to frontline workers, encouraging everyone to contribute to the improvement process.
3. Focus on Process:
– Process Over Results: The Kaizen approach emphasizes improving processes rather than merely focusing on end results, as better processes naturally lead to better outcomes.
4. Small, Incremental Changes:
– Steady Progress: Kaizen advocates for making small, manageable changes regularly rather than waiting for large, dramatic overhauls.
5. Standardization:
– Creating Baselines: Once an improvement is made, the process is standardized, setting a new baseline for further improvements.
6. Problem-Solving:
– Identify and Eliminate Waste: Kaizen encourages identifying inefficiencies, waste, and issues in the process, then systematically solving them.
7. Team-Oriented Approach:
– Collective Effort: Kaizen fosters teamwork, with employees working together to brainstorm, implement, and sustain improvements.
8. Visual Management:
– Transparency: Tools like visual boards and charts are used to make progress visible and ensure everyone is aware of ongoing improvements and goals.
9. Long-Term Commitment:
– Cultural Shift: Kaizen requires a long-term commitment and a cultural shift within an organization, integrating continuous improvement into the company’s ethos.
10. Global Impact:
– Adopted Worldwide: The principles of Kaizen, initially applied in Japanese manufacturing, have been adopted globally across various industries, contributing to Japan’s competitive success on the world stage.
This book highlights how the Kaizen philosophy has played a crucial role in Japan’s post-war economic recovery and global competitiveness by fostering a culture of continuous improvement and collective responsibility.